冲击地压是威胁矿井安全生产的主要灾害类型之一,治理措施包括提前预防和被动解危两个方面。提前预防是指采用合理的开采设计来防治冲击地压的发生;被动解危主要包括钻孔卸压、煤层注水、爆破卸压、掏槽卸压、顶板预断裂、定向裂缝法等。在被动解危措施中,钻孔卸压是目前应用最为广泛的措施之一。钻孔卸压主要针对煤层,通过在煤层中人为施工大孔径卸压钻孔,利用钻孔的变形破坏,释放聚集在煤体内部的弹性变形能,消除或减缓冲击地压危险性。作为煤层钻孔卸压的主要钻具之一的钻头,主要有孕(表)镶金刚石钻头、聚晶金刚石复合片钻头(简称“PDC钻头”)、硬质合金钻头。
PDC钻头因具有低钻压、高转速的优点,得到了广泛应用,国内外研究人员在此方面做了较多的研究。余静、马清明、祝春生、许爱等通过实验和数值模拟手段分析了PDC切削齿受力和破岩规律;韩来聚、韦忠良、张晓亮等对PDC取芯钻头切削齿载荷进行了实验研究及仿真分析,得出了PDC取芯钻头的应力应变分布规律;谢晓红、汪冰峰等对PDC取芯钻头切削齿破岩时的磨损规律进行了研究;顾大钊等采用相似材料模型试验对行星钻头的破岩机理及破岩过程进行了研究;张光辉运用理论分析和数值模拟方法对钻齿压入岩体做了系统的研究。当前关于PDC钻头研究主要集中在钻头破岩机理、切削齿破岩的力学分析、钻削破岩的数值模拟等方面,而对于钻头的优化改进方面研究较少。基于此,本文以徐矿集团煤层钻孔卸压使用的PDC钻头为研究对象,优化改进钻头,达到扩孔,提高钻进效率的目标。
2 原PDC钻头存在的问题及拟解决方案
徐矿集团煤层钻孔卸压原使用的PDC钻头为φ127mm三翼无芯金刚石复合片钻头,如图1所示:
图1 三翼无芯金刚石复合片钻头
(1)开孔角度不易掌握,易偏斜,常出现1次开孔不成功,需多次开孔的情况,存在无效钻进时间。
(2)钻头开孔直径φ127mm,破煤面积大,钻进3~5m时即出现煤炮、吸钻、卡钻等钻孔动力效应,钻进时间加长。
(3)退钻时孔内堆积的钻粉不能破碎排出,易出现卡钻,增加钻进时间。
(4)钻孔动力效应大时,排粉量大,可能出现排渣不顺畅的情况,增加钻进时间。
通过分析以上原因可知,要提高卸压钻进效率,拟从钻头结构和钻头喷嘴两个方面采取三种改进措施:
(1)逐级扩孔。针对前两种问题,可通过钻头结构的改进加以解决,思路是把单层3个切削翼的钻头改进为多层多翼结构,由上至下各层切削翼直径逐步增大。
(2)退钻切削。解决第3个问题的思路是在最大孔径的切削翼后端增加1层小孔径的退钻切削翼,将堆积的钻粉颗粒切削变小,可顺畅地排出钻孔。
(3)增大水量。解决第4个问题,可采取增加喷嘴数量、加大钻头喷嘴直径,增加钻头喷出的水量,在动力效应大、排粉量大时不出现钻粉堵塞、排渣不畅等问题。
2 钻头结构优化技术
根据逐级扩孔、退钻切削的思路,将三翼无芯金刚石复合片钻头优化设置为正向3层切削翼,直径分别为75mm、108mm、129mm,每层3个切削翼;设置1层3个退钻切削翼,直径为108mm,组成4层12翼金刚石复合片钻头,如图2所示。根据多次现场试验,对钻头其他结构进一步改进如下:
(1)为有利于排渣,根据钻头旋转方向,设计了自上向下每层切削翼与钻头基体相错布置,使原本直线布置的上下切削翼间按逆时针方向螺旋布置,与钻头旋转方向匹配,有利于提高钻进效率。如图2所示:
图2 4层12翼PDC钻头
(3)每层切削翼的外缘需弧形布置,保证每层切削翼外缘均在相应直径的一个圆周上。
(4)为减小排屑槽的阻力,切削翼的背部设计为平滑过渡。
改进后的钻头由小至大递进扩孔,退钻切削翼破碎堆积的钻粉颗粒,防止埋钻,将该钻头的命名为4层12翼金刚石复合片扩孔防埋钻头。
3 大流量通水优化技术
3.1 原钻机钻具通水系统通水孔面积
要使切削的钻粉顺利排出钻孔,除从钻头结构优化外,另一种办法是增加钻头喷出的水量,用大流量的水将钻粉带出钻孔。钻头喷出的水量,由钻头喷嘴数量和喷嘴直径、钻头基体通水孔径、钻杆通水孔径、外接水龙头通水孔径等5个方面控制。根据前述原钻机钻具配置各通水部件的通水孔面积为:φ127mm无芯金刚石复合片钻头喷嘴通水孔面积之和为546mm2、钻头基体通水孔面积为254mm2;φ73mm深槽双螺旋钻杆通水孔面积为314mm2;Q73水龙头通水孔面积为254mm2;外接水管通水孔面积为490mm2。系统通水孔面积由孔径最小的通水孔面积决定,即原钻机钻具通水孔面积为254mm2。
3.2 钻杆和水龙头通水孔径优化
因φ73mm深槽双螺旋钻杆通水孔径为20mm,在不改变钻杆材质、结构的情况下,根据多次实验,通水孔径只能由20mm扩大为22mm,如果再扩大,强度、扭矩变小,CMS16200/80钻车无法匹配使用该种钻杆。因此,将φ73mm深槽双螺旋钻杆通水孔径优化后确定为22mm。
根据φ73mm深槽双螺旋钻杆扩大后的通水孔径22mm,Q73水龙头通水孔径也确定为22mm。这样,可满足水龙头抗高压水的能力和密封性等要求,也不需改变水龙头材质、增加重量。
φ73mm深槽双螺旋钻杆通水孔和Q73水龙头通水孔面积为380mm2。
3.3 钻头喷嘴优化
扩大钻头的通水孔径,首先需把钻头基体的通水孔径由18mm扩大到22mm,经现场制作、计算和试验,钻头基体通水孔径扩大到22mm后,钻头的强度、扭矩能满足配合CMS16200/80钻车的要求。钻头通水孔面积的优化主要是优化钻头喷嘴的数量、位置、孔径。具体方案为:在直径75mm的第1层钻头顶端设置1个直径16mm的喷嘴和2个直径6mm的喷嘴,在3个排屑槽各设1个直径12mm的喷嘴,共6个喷嘴,如图3、图4所示:
图3 钻头顶端喷嘴
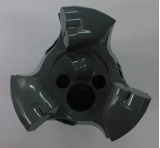
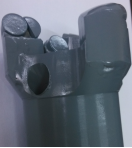
钻头喷嘴优化后通水孔面积之和为502mm2。
3.4 优化前后通水部件通水孔面积比较
外接水管通水改为孔径为25mm,通水孔面积为490mm2。这样在钻头基体和钻头喷嘴、深槽双螺旋钻杆、水龙头改进后,各通水部件的通水孔径面积最小为钻头基体、钻杆和水龙头的通水孔径面积,3个均为380mm2,因此该通水系统的通水孔面积为380mm2。与改进前通水孔面积254mm2相比,改进后通水孔面积是改进前的1.5倍。
4 现场试验及应用
4.1 试验地点工程概况
徐矿集团张双楼煤矿74101工作面位于该矿东一采区,74101材料道埋深-950m,设计全长1602m,至2016年3月3日已掘进1192m。该头掘进评估为强冲击危险,直接顶为泥岩,基本顶为中砂岩,煤厚平均为3.5m,采用煤巷锚网索支护。
根据防冲措施,74101材料道迎头共布置5个卸压钻孔,巷帮间距2m布置1个卸压孔,卸压孔布置如图5所示。在该巷道试用4层12翼金刚石复合片扩孔防埋钻头施工卸压孔。
图5 卸压孔布置图
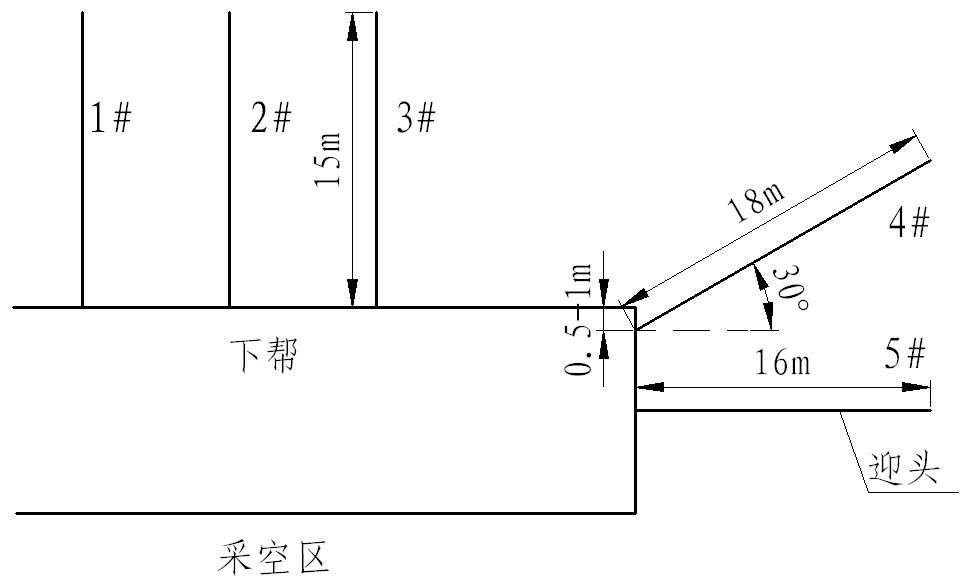
4.2 试验效果
本次试验采用CMS1-6200/80型煤矿用液压深孔钻车配备φ73mm深槽双螺旋钻杆,分别试用φ129mm的5层15翼金刚石复合片防埋扩孔钻头施工1#卸压钻孔,用φ127mm的1层3翼无芯金刚石复合片钻头施工2#卸压钻孔,采用φ129mm的4层12翼金刚石复合片扩孔防埋钻头施工3#~5#卸压钻孔,对比钻进时间、分析钻进效率。试验效果如下:
(1)4层12翼金刚石复合片扩孔防埋钻头开孔时明显比3翼无芯金刚石复合片钻头和15翼金刚石复合片防埋扩孔钻头快、稳,成孔直线度好。
(2)现场测试,4层12翼金刚石复合片扩孔防埋钻头通水系统流量是3翼无芯金刚石复合片钻头的1.3~1.5倍。由于水流量增大,现场排渣顺畅,出现卡钻的次数减少,达到了扩孔防埋的效果。
(3)在同等压力条件下,4层12翼金刚石复合片扩孔防埋钻头单孔钻进用时比3翼无芯金刚石复合片钻头节约8~10min。
4.3 应用情况
4层12翼金刚石复合片扩孔防埋钻头在74101材料道试验成功取得较好效果后,在2016年3月10日在74101运输道试用,也取得较好效果。至2016年7月30日74101材料道和运输道使用4层12翼金刚石复合片扩孔防埋钻头,累计施工煤层卸压钻孔820个,累计钻深17926m。
4.4 效益分析
2016年3月27日至4月18日在74101材料道试用期间,1个4层12翼金刚石复合片扩孔防埋钻头累计施工卸压孔84个,3翼无芯金刚石复合片钻头平均每个钻头施工钻孔48个,1个钻头多施工36个钻孔。
(1)2016年3月10日至7月30日74101材料道和运输道施工煤层卸压钻孔17926m,累计消耗4层12翼金刚石复合片扩孔防埋钻头12个,平均每个钻头可钻进1493m;3翼无芯金刚石复合片钻头平均每个可钻进720m,钻头耗损率降低51.8%。
(2)施工煤层卸压钻孔17926m,消耗多翼金刚石复合片防埋扩孔钻头12个,合计价格为2.88万元;如使用3翼无芯金刚石复合片钻头预计消耗25个,合计价格3.9万元,节约1.02万元。
5 结论
(1)在钻头结构和通水系统等方面优化改进后,4层12翼金刚石复合片扩孔防埋钻头具有逐级扩孔、退钻切削的优点,系统通水孔面积是改进前的1.5倍,达到了卸压钻进扩孔防埋的效果。
(2)在同等压力条件下,4层12翼金刚石复合片扩孔防埋钻头钻进总用时比3翼无芯金刚石复合片钻头节约8~10min,钻头耗损率降低51.8%。
(3)4层12翼金刚石复合片扩孔防埋钻头已取得实用新型专利,并具有广阔的应用前景。
参考文献
[1]窦林名,何学秋.冲击地压理论与技术[M].徐州:中国矿业大学出版社,2001.
[2]余静.岩石机械破碎规律和破岩机理模型[J].煤炭学报,1982,7(3).
[3]马清明,王瑞和.PDC切削齿破岩受力的数值模拟研究[J].钻采工艺,2006,29(4).
[4]马清明,王瑞和.PDC切削齿破岩受力的试验研究[J].中国石油大学学报(自然科学版),2006,30(2).
[5]祝春生,王镇全,邢树宾,等.PDC钻头切削齿受力模拟实验装置研究[J].石油机械,2008,36(2.
[6]许爱.PDC钻头切削齿破岩载荷规律的分析[J].探矿工程-岩土钻掘工程,2006,33(7).
[7]韩来聚,陈庭根,须志刚.全尺寸PDC钻头切削齿载荷分布规律的实验研究[J].石油大学学报(自然科学版),1992,16(6).
[8]韦忠良,陈庭根.PDC钻头钻进时扭矩影响因素研究[J].石油钻探技术,1995,23(1).
[9]谢晓红.PDC取芯钻头切削齿磨损规律的研究[D].长沙:中南大学,2011.
[10]汪志明,孙清德,于军泉,等.超高压双流道PDC钻头破岩机制研究[J].岩石力学与工程学报,2007,26(4).
[11]顾大钊.行星钻头破岩机理及过程的试验研究[J].中国矿业大学学报,1990,19(3).
[12]张光辉.PDC钻头破岩机理及围岩状态识别技术研究[D].徐州:中国矿大大学,2015.